Social
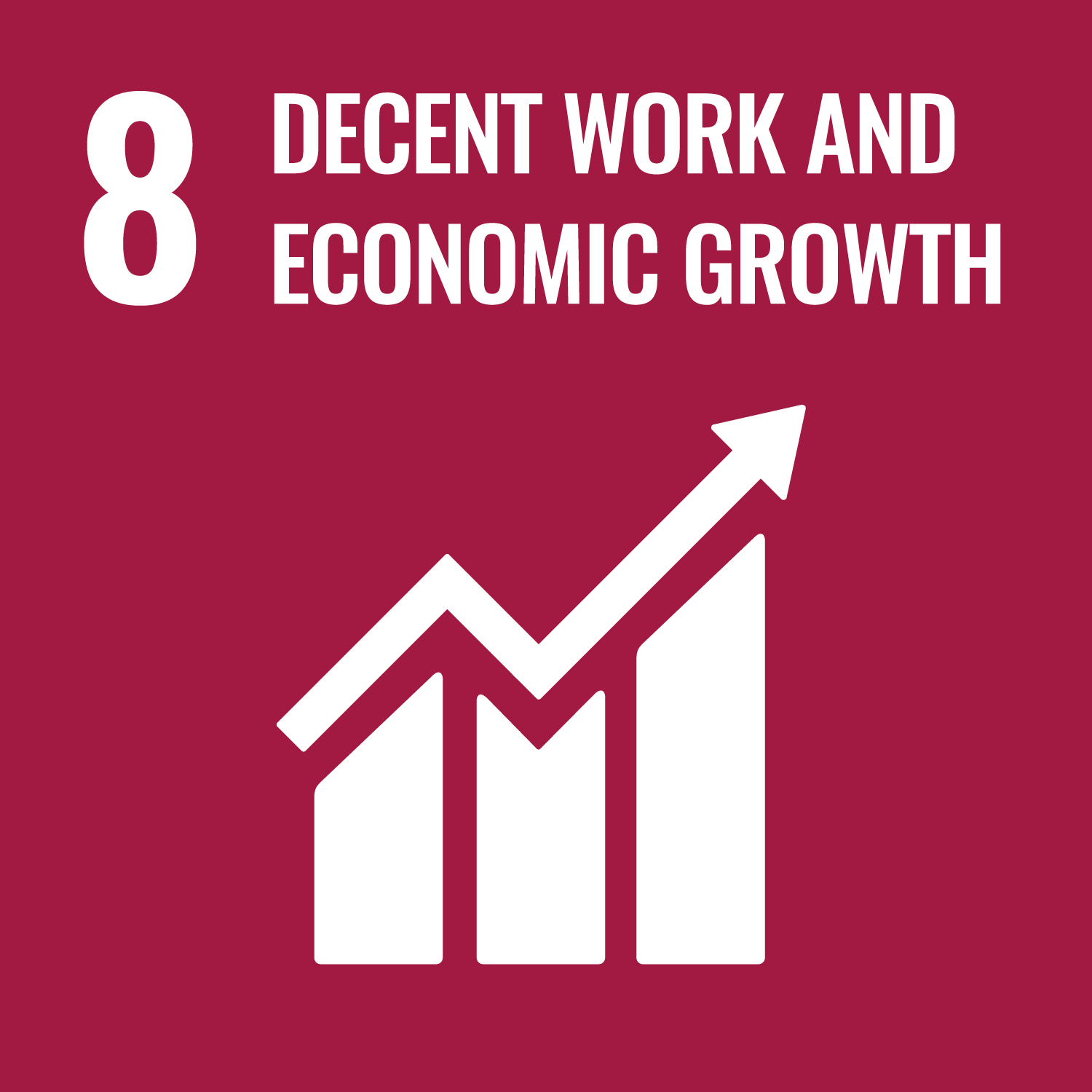
Own Workforce
PWT Group aims to be an attractive workplace, and we focus on recruiting, educating and retaining our employees. Through ongoing dialog regarding continuing education, we ensure that our employees have the right qualifications we need. The need for education and personal development is clarified annually. Upskilling of employees benefits both our employee and our business.
The well-being of our employees is important and through our working environment committee we work to ensure good and safe working conditions for all employees.
Supply Chain
The production of our products takes place in countries across the globe. PWT Group does not own any factories but cooperates with a range of suppliers, both directly at production facilities and via sourcing houses. The top 30 factories represent approx. 89% of all orders, and our focus is primarily given to these.
PWT Group aims for supplier cooperation based on mutual understanding, trust and long-term relationships. Cooperation on social responsibility and environmental protection is an essential part of the relationship with suppliers.
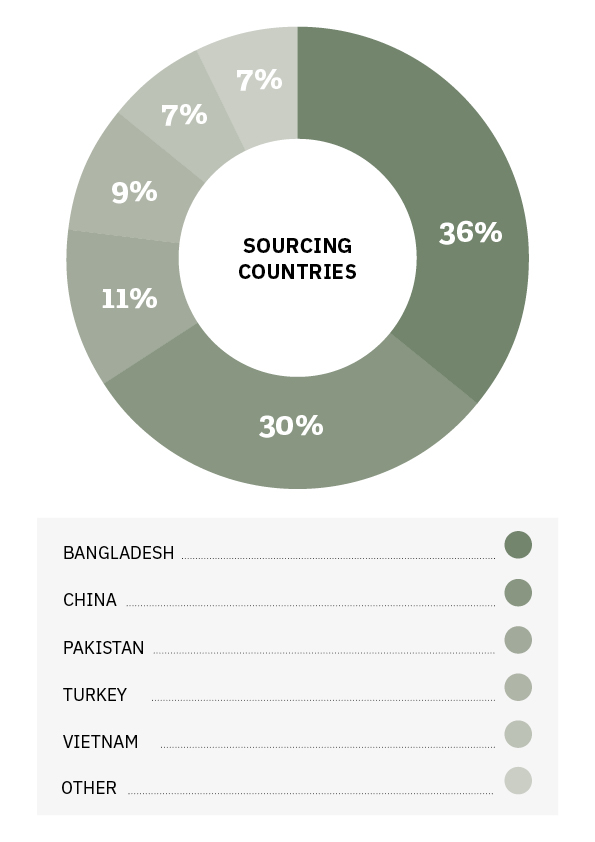
It is of utmost importance for us that our textiles are produced at factories with decent and safe working conditions. Many resources are spent on following up with suppliers on their work on adhering to our Code of Conduct.
Our Code of Conduct is based on Danish Fashion & Textile’s Code of Conduct and describes the sustainability minimum standards set for business partners.
We are aware that some production countries represent systemic risks of unsafe working conditions and challenged labour rights. At the same time, the textile industry creates millions of jobs, and we do not see it as an option to cut out countries from the sourcing loop. Instead, we focus on contributing to improvement, through the supply chain work, and through participation in national and international initiatives. Read more about our engagement in initiatives here
Amfori BSCI
We have been a member of the amfori since 2013 and the amfori BSCI platform is actively used as the main social audit system. Suppliers are expected to work with the amfori BSCI (SA8000 or similar system) and in cases where a factory has not yet initiated the BSCI process, we expect them to join within a reasonable time. Suppliers are audited annually by third party auditors, and we use the audit reports to promote dialogue on necessary improvements. In the amfori BSCI system, a supplier can get the result A-E. Acceptable level is A, B or C.
See below figure showing our top 50 suppliers BSCI performance
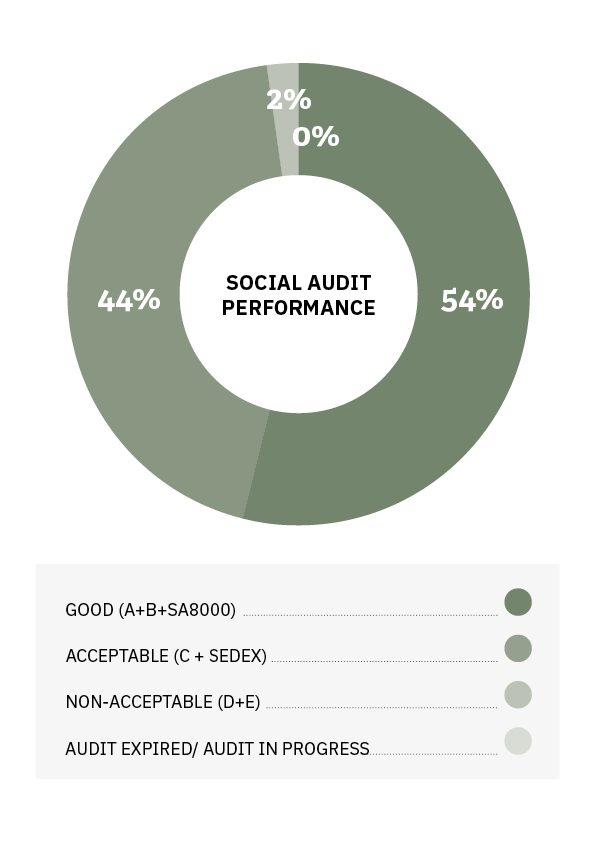
We have set up a systematic follow-up system on audit reports. This means that when we receive a new report from a supplier, we go through it, and then create a so-called CAP-form, which mentions findings from the report. This CAP-form is sent to the supplier, and we expect them to fill out CAPs (corrective action plans) for each issue, including a timeframe for each improvement project. In this way, we track the improvements from supplier side (or the lack of such).
We do not expect suppliers to overcome challenges overnight, but we focus on their ability and willingness to demonstrate continuous improvements, and we feel confident that cooperation and dialogue will result in valuable partnerships.
The international Accord for Health and Safety in the Textile and Garment Industry.
PWT has been a signatory member of the Accord since 2013, and we signed the new updated agreement for The International Accord for Health and Safety in the Textile and Garment Industry in Bangladesh for six more years.
As such, we continue to require all active Bangladeshi suppliers to work actively with the RMG Sustainability Council (RSC). This meaning 1) engaging with the Inspection Programme, 2) improving fire, building and electrical safety based on inspection findings, 3) participating in the extensive training, and 4) engaging in remediation dialogues based on the RSC grievance mechanism.